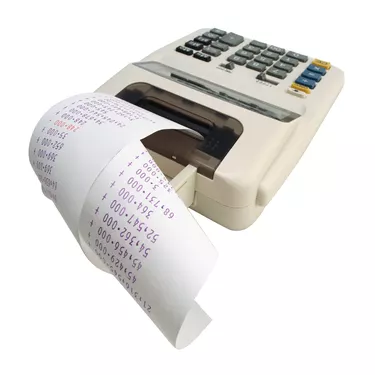
Customers want products to perform better, cost less and work properly for longer. They want quality. Ensuring your quality system works falls to the business owner, who can use customer inspections, ISO registration or internal audits based on quality costs, customer response or errors to quantify, test and measure the system's effectiveness.
Quality Reports
Video of the Day
The International Organization for Standardization, which publishes quality management standards, says quality records demonstrate how effectively a quality department or quality management system works. You can conduct your own internal quality audits, invite your customers to inspect your quality reports or arrange for a third-party inspection. Third-party inspections, conducted by organizations the ISO designates as registrars, provide a certification attesting to your compliance with ISO standards.
Video of the Day
Quality as Dollars
If you choose to conduct an internal audit of your quality system, you can approach the audit by quantifying quality efforts in financial terms. Value measurements that demonstrate a quality system's effectiveness in terms of sales per employee or rework and scrap costs clearly display the cause-and-effect relationship between quality and profit, using familiar financial terms. If your company hemorrhages dollars in scrap and the costs of reworking parts at an ever-increasing rate, that is a clear indication of your quality system's effectiveness.
Product Error Rate
Quality depends on using the proper machinery, good materials and well-trained employees using proper production methods, explains Masaaki Imai, author of "Kaizen: The Key to Japan's Competitive Success." Kaizen is the basis of the continual quality improvement in the Toyota Production System. Four elements -- workers, materials, machines and methods -- must work in concert to produce quality. According to the Lean Enterprise Institute, product errors in most industries average between 2 percent and 5 percent of production. If you experience a product error rate greater than 5 percent, your quality system has failed to resolve a problem with those four elements.
Consumer Responses
Total quality management systems use customer satisfaction as a yardstick. Just as restaurants use customer comment cards to improve their performance, you can evaluate the effectiveness of your company's quality effort by the level and nature your customers' satisfaction. This direct feedback, while not a full-blown audit of your quality system, highlights issues that your quality department should address.